Una fabbrica ripensata da Renzo Piano. Un esercito di 48 robot. Investimenti per 300 milioni di euro. A Settimo Torinese, Pirelli progetta il futuro. Ripartendo dagli pneumatici e da una tecnologia molto speciale.
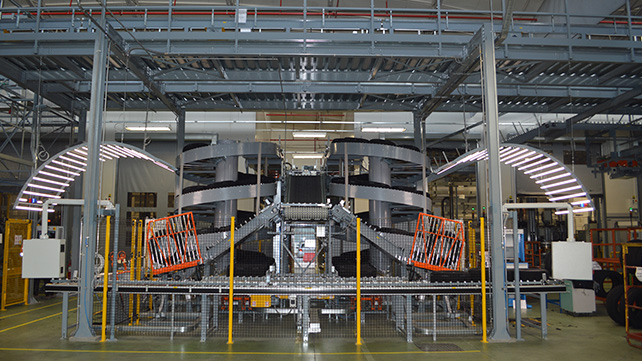
Se pensate che i robot ci ruberanno il lavoro, andate a fare un giro a Settimo Torinese. Armatevi di calcolatrice e preparatevi a moltiplicare: il numero di persone impiegate e il valore generato. Se l’innovazione è reale, le sottrazioni non esistono. Questione di aritmetica, ma soprattutto di filosofia: quella che ha trasformato il Polo piemontese di Pirelli in un avanzato esempio di Industria 4.0, da fabbrica che sfornava pneumatici comuni a paradigma di gestione digitalizzata, efficiente e flessibile per la creazione di modelli di alta e altissima gamma. Non più semplici manufatti standardizzati, ma oggetti intelligenti, disegnati con i clienti per rispondere alle specifiche esigenze e poi realizzati in modo tracciabile in ogni passaggio.
L’evoluzione è figlia di un processo di trasformazione iniziato nel 2009 e pienamente a regime da un paio di anni, per cui Pirelli − colosso da 5,2 miliardi di euro di fatturato e 31 mila dipendenti nel mondo − ha investito 300 milioni di euro, reclutato Renzo Piano, puntato sulla sostenibilità e coinvolto le istituzioni locali. Insomma, un progetto rotondo per traghettare il business nel futuro: non per niente, il ritorno in Borsa del Gruppo nel 2017 è stato costruito prospettando agli azionisti un nuovo concetto, alto, immaginifico e futuribile, di produzione. A partire da quella consentita da Next Mirs, la tecnologia proprietaria, brevettata nel 2010 e figlia di investimenti annui in Ricerca e Sviluppo superiori al 6% dei ricavi derivanti dall’alta gamma, utilizzando software e macchine italiane, con cui a Settimo si ottengono gli pneumatici cosiddetti Prestige: Ferrari, Lamborghini, Maserati, Mercedes-amg, Audi RS e altri oggetti del desiderio.
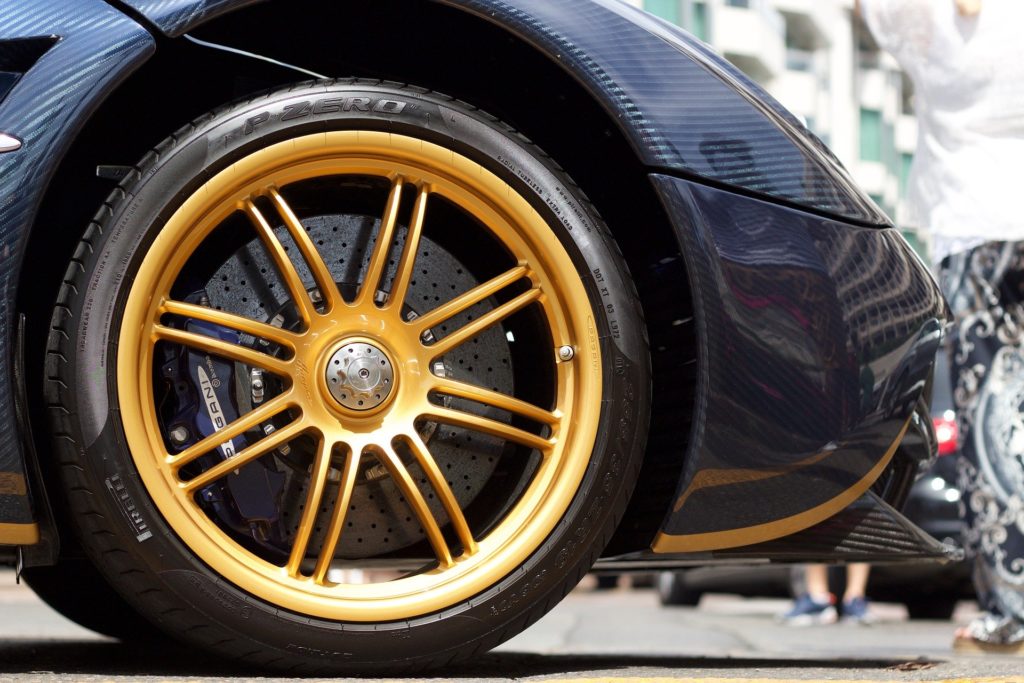
Qui, in una specie di laboratorio del lavoro che sarà, 48 robot rispondono alle esigenze produttive in modo granulare: «Se negli altri reparti si opera su lotti più grandi, da 250 o 100 pezzi alla volta, qui le macchine sono in grado di realizzare un lotto di un singolo pneumatico»,
I ROBOT NON HANNO RIMPIAZZATO GLI UMANI, ANZI: NE HANNO ANCORA BISOGNO, PIÙ CHE NELLE CATENE TRADIZIONALI
Spiega Francesco Sala, Executive Vice President Technical Operations Pirelli. Può sembrare banale, ma non lo è. Dalla rivoluzione industriale in poi la redditività si basa sulle economie di scala: essere efficienti sul singolo pezzo significa avere rivoluzionato le regole del gioco. «Dal Next Mirs escono ogni anno centinaia di migliaia di pneumatici, sotto la supervisione di 120 operatori altamente formati, che conducono la linea e si occupano di problem solving». Nel resto del Polo sono impiegate circa 1.110 persone per circa 4 milioni di pezzi annui. Basta fare di conto: non solo i robot non hanno rimpiazzato gli umani, ma ne richiedono un numero maggiore rispetto alle produzioni tradizionali. La questione, però, non si può ridurre ai soli numeri. «Quello che ci interessa è l’innalzamento delle competenze.
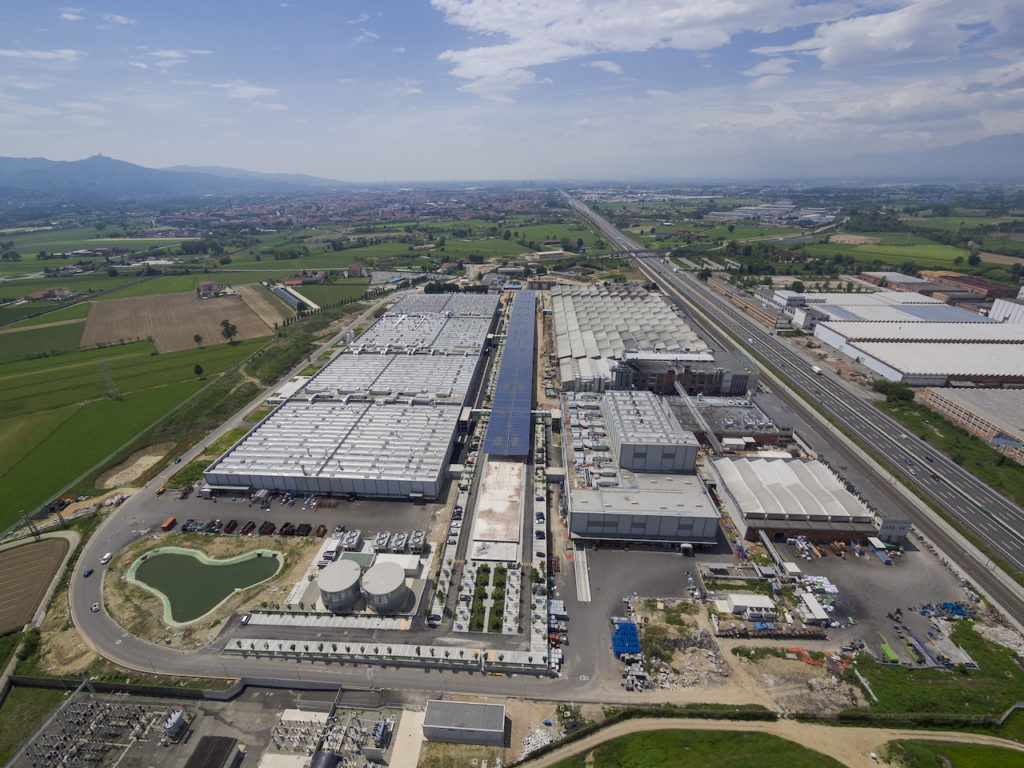
Per noi le persone hanno un ruolo cruciale e per governare un reparto interamente robotizzato ci vogliono giorni di training», precisa Sala. «Abbiamo insomma operai capaci di affrontare la trasformazione con consapevolezza e questo permette loro di gestire le complessità del processo e del prodotto». La gestione della complessità è il leitmotiv della rivoluzione di Settimo Torinese, il fil rouge con cui, prima del grande salto nella nuova era, i dipendenti sono stati sottoposti a 24 giorni di formazione che hanno trasformato la mentalità aziendale: «Basta un dato: l’assenteismo si è drasticamente ridotto». Percorrendo “La Spina”, il corridoio sormontato da pannelli fotovoltaici progettato da Renzo Piano per collegare le due unità produttive che componevano la vecchia fabbrica, non è difficile comprendere il perché. Sorpassata la biblioteca che contiene 5 mila volumi, inserita nel circuito dei prestiti comunali, si arriva al campo da calcetto, disponibile per tutti; in primavera, la lunga navata è colorata dalla fioritura dei 400 ciliegi che corrono paralleli all’edificio, incorniciati dalle ampie vetrate che sostituiscono le pareti.
E da cui la luce filtra persino nel cuore della produzione,
7 TIPI DI GOMMA E ALTRE MATERIE PRIME − PER 200 TONNELLATE UTILIZZATE OGNI GIORNO − CREANO LA MESCOLA DI ALTISSIMA QUALITÀ DI CUI È COMPOSTO OGNI PNEUMATICO
laddove sette diversi tipi di gomma e altre materie prime − per 200 tonnellate utilizzate ogni giorno − creano la base della mescola di altissima qualità di cui è composto ogni pneumatico che esce da Settimo. «Tutto è collegato: la sostenibilità ambientale e quella economica, la bellezza della fabbrica in cui è piacevole lavorare con la sicurezza e l’innovazione. È una questione di mentalità, ramificata in ogni aspetto del Polo», spiega Sala. Non per niente, il 97% dei rifiuti prodotti è avviato a recupero.
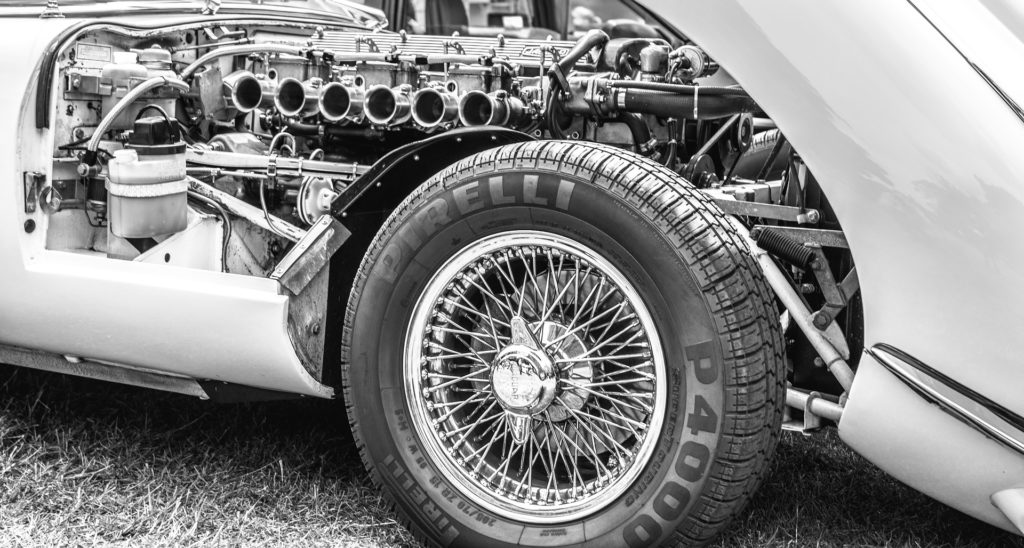
Lo hanno chiamato Pirelli Smart Manufacturing, produzione intelligente. Significa anche che ogni pezzo ha un codice grazie al quale è possibile andare a ritroso per conoscerne le componenti, le lavorazioni, persino gli addetti che le hanno eseguite. Per studiare ogni possibile problema, risolverlo in tempo reale e diventare materiale utile per le quasi 80 persone che lavorano localmente (su un totale di circa 1.900 nel mondo) alla Ricerca e Sviluppo. La gestione in tempo reale, d’altronde, è parte integrante della mutazione dello stabilimento: «Una volta solo i responsabili dei reparti avevano i telefonini per comunicare; oggi sono disponibili anche per gli operai. E soprattutto abbiamo software e app utili a interagire tra reparti, ma anche tra diverse fabbriche e persino con i clienti».
Gli applicativi segnalano approvvigionamenti e scorte, aiutano a pianificare la produzione di concerto con gli altri reparti e con gli ordini dei clienti. I dati di ogni segmento, ma anche di ogni fabbrica Pirelli, sono disponibili in un supercloud con cui analizzare eventuali problemi e cercare risposte alle criticità. Se ne discute in stanze vetrate collocate in ogni reparto: perché le informazioni sono essenziali, ma lo scambio, il pensiero e il confronto lo sono anche di più. Comunicazione e flessibilità come base della fabbrica: chissà cosa ne avrebbe detto Henry Ford. Ma il tempo passa. E il treno del futuro, ogni tanto, parte proprio da casa nostra.
OGNI PEZZO HA UN CODICE PER RISALIRE ALLE COMPONENTI, ALLE LAVORAZIONI E AGLI ADDETTI CHE LE HANNO ESEGUITE
Tratto dall’articolo di GQ Italia.